Butt Welding Machine Used to Weld Broken Wires During the Drawing Process
The butt welding machine is a common resistance butt welding machine that achieves firm welding of metal wires through resistance heating and pressure and achieves efficient welding of metal materials through precise current control and pressure regulation. Proper use and maintenance of this equipment can significantly improve production efficiency and welding quality.
Butt welding machines are widely used in wire drawing production lines and other metal processing processes. During the wire drawing process, the butt welding machine welds together broken steel wires or steel wires that need to be extended to ensure the continuity of drawn wire production.
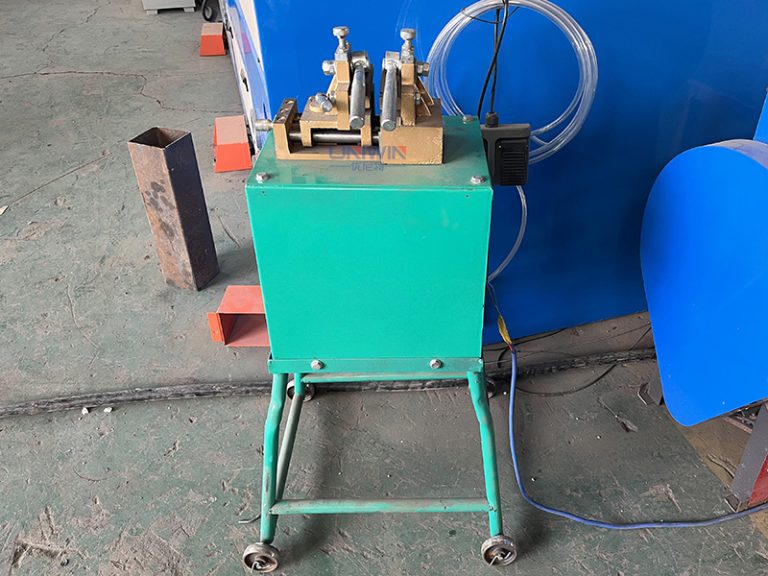
Specification of Butt Welding Machine
Model | Rated Capacity | Primary Voltage | Welding Diameter (Low Carbon Steel) |
---|---|---|---|
UN-4 | 4KVA | 220V | 0.3-3mm |
UN-7 | 7KVA | 380V | 1.5-6.5mm |
UN-12 | 12KVA | 380V | 2-8mm |
Use and Maintenance of Butt Welding Machine
Working Principle
The working principle of the butt welding machine is based on resistance welding technology. The main working process is as follows:
- Preparation: Clamp the two pieces of metal wire to be welded between the electrodes.
- Heating: Apply electric current through electrodes rapidly heats the metal at the contact point to its melting point.
- Pressure: As the metal melts, the electrodes apply pressure to fuse the molten metal together.
- Cooling: Cut off the current and maintain the pressure for a while to allow the welding point to cool and solidify to form a strong welded joint.
Maintenance
Clean the electrode surface regularly to prevent oxides and impurities from affecting the welding quality.
Check cables and connectors regularly to ensure stable current transmission.
Regularly lubricate the transmission parts of the equipment to reduce wear and extend its life.
Check the cooling water pipes and fans to ensure the cooling system is operating properly.
Advantages of Butt Welder/Butt Welding Machine
The heating time is short, and the heat is concentrated, so the heat-affected area is small, and deformation and pressure are small. Moreover, the parameters of the butt welding machine are adjustable, the welding process is controlled, and the welding quality has good repeatability and consistency.
The butt welder can complete the welding process in a short time, significantly improving production efficiency. It is especially suitable for scenarios that require continuous production, such as steel wire drawing, steel bar processing, etc.
The machine is suitable for welding various metal materials, such as steel, copper, aluminum, etc., and has a wide range of applications.
The parameters such as welding current, welding time, and pressure are adjustable, which can adapt to the welding requirements of different workpieces and have high flexibility.
Welding does not require filler metals such as welding wires and electrodes, and the welding cost is low. And because the welding quality is high and stable, the scrap rate is low, reducing production costs.
It is simple to operate and easy to maintain, reducing the operator’s skill requirements.
No noise and harmful gases are produced during welding, which improves working conditions and is suitable for use in various environments.
The equipment uses the principle of resistance heating, has a high energy utilization rate, and is more energy-saving than other welding methods.
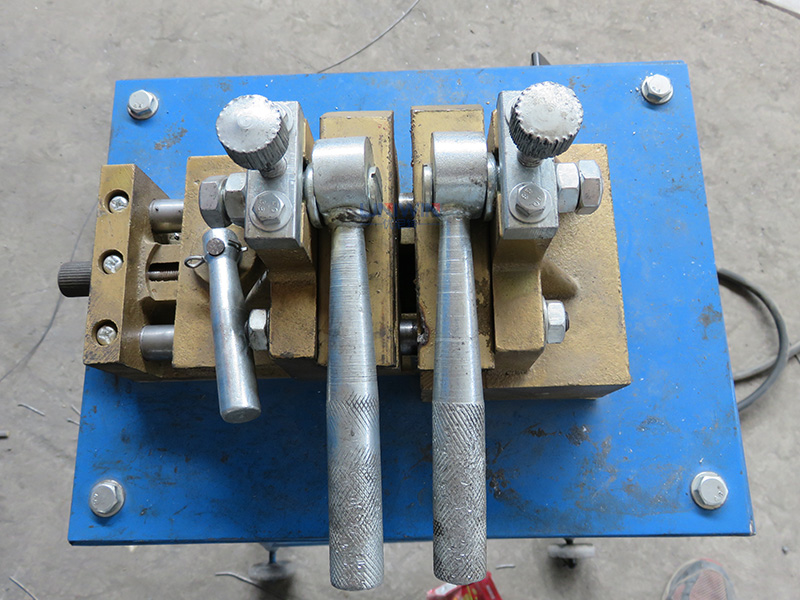
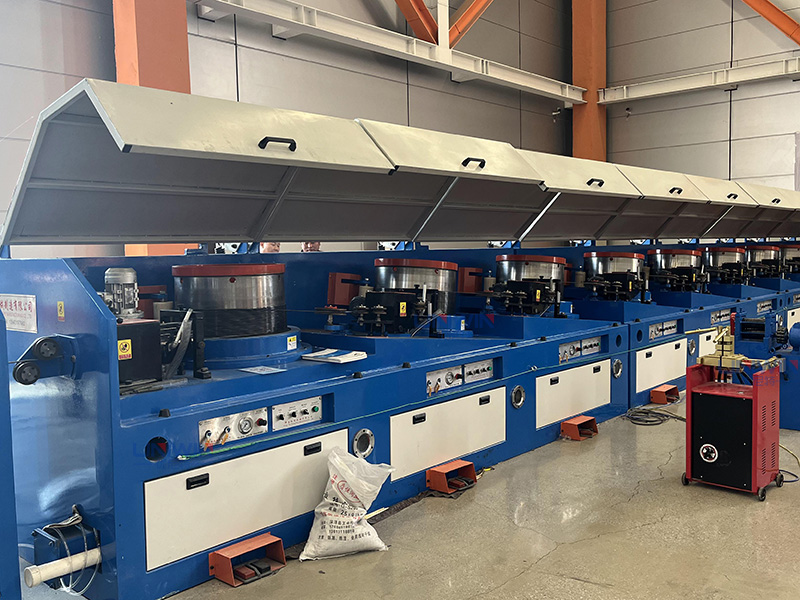
Butt Welding Machine Application
- Wire Drawing Production Line: During the steel wire drawing process, broken steel wires are welded, or new steel wires are connected to ensure the continuity of production.
- Metal Processing: Weld various metal wires, such as copper wires, aluminum wires, etc., suitable for cable manufacturing, electronic components, and other industries.
- Steel Bar Welding: Used for steel bar connection in construction projects to improve the overall strength and stability of the building structure.
- Cable Manufacturing: Suitable for welding cables and wires to improve the reliability and conductivity of connection points.